In stage I of the project were developed mainly research activities related to data analysis methods of emissions reduction in turbo-engine with injection of fluids and correlation with the afterburning, respectively site selection for the customer experience (Petrom OMV Group).
Between possible testing locations for technologie, the best is 2xST 18 cogeneration power plant.
During stage II of the project were developed mainly research activities related to defining technical solutions for integrated turbo-engine - afterburning, the development thermomechanical scheme, project afterburning burner for the beneficiary, data sheets, technical solutions for the injection of fluid in turbo-engine.
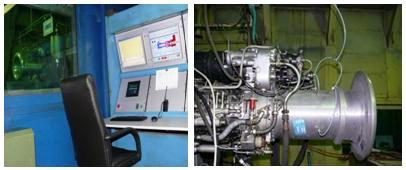
Control room to stand and turbo-engine at INCDT COMOTI mounted test
Technical-scientific results of stage II is focused on: technical solution for integrated system= 1pc; scheme thermomechanical = 1 pc; technical project burner = 1 pc, data sheets = 2 pcs, technical solutions in principle on fluid injection in various turbo-engine alternatives (water injection, that steam = 2 variants), for emissions reduction and increased efficiency = 1 pc., disseminating researches results = 2 scientific papers.
Stage III
In the stage III of the project were developed mainly for research activities related to execution of technical project for water injection turboengine – afterburner test bench, numerical modeling of processes at the water injection into turboengine combustion chamber, technical solutions in the field of burners with fluid atomizer, technical design for implementation of water injection system into ST 18 turboengine from beneficiary (PETROM Grup OMV), making the water spray atomizer in the combustion chamber of the turboengine - afterburner and laboratory tests, achievement afterburning chamber for water injection – afterburner test bench, afterburner modules making (spare parts) for the installation of the beneficiary (PETROM Grup OMV).
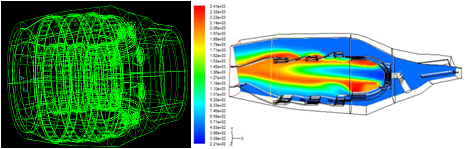
Modeling of the combustion chamber on turboengine TV 2 – for water injection
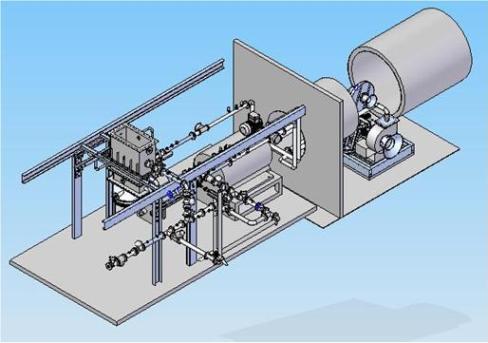
3D model of the test bench for afterburning installation from INCDT COMOTI
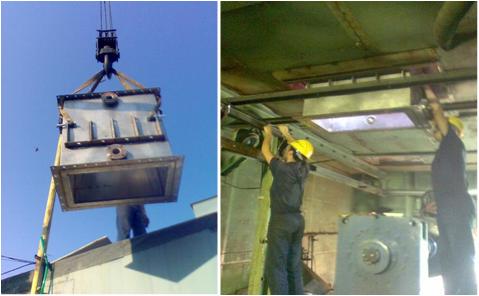
Montage of afterburning chamber from the test bench at INCDT COMOTI
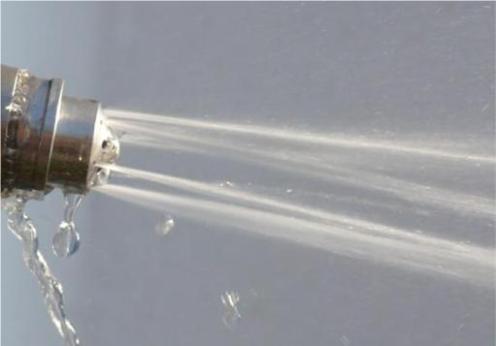
Burst water obtained by pumping water through the nozzle holes corresponding dual atomizer
Technical and scientific results of stage III is focused on: product Turboengine TA2-GN duplex = 1 set (conceptual model); afterburning module manufacturing technology - a laboratory level = 1 pc; technical project on water injection – afterburner test bench = 1 pc.; preliminary numerical model on water injection into turboengine = 1 pc; solutions principle of noxes reduction and increase in turboengine efficiency by injecting fluid, the effects on afterburning = 1 pc., the technical data of spraying fluid = 1 set, technical project part thermomechanical, water injection - adjustable afterburner system = 1 pc., engineering design automation side, water injection - adjustable afterburner system = 1 pc., fuel - water atomizer ( physical object) = 1 pc; jet spray experimental data = 1 set, afterburning chamber for test bench (physical object) - mounted on position = 1 pc; afterburning modules (physical object - spare parts) = 3 pieces; disseminating researches results = 5 scientific papers (3 papers ISI).
Stage IV
In the fourth stage of the project were mainly conducted the research and experiments related to the adaptation of test bench for water injection in gas turbine – afterburner system, afterburner - water injection numerical model development, documentation for test bench, technical project, related to assembly of thermomechanical and automation, for water injection into gas turbine from the Beneficiary, analysis of the behavior for modules of afterburner in industrial conditions - spare parts, development of technology systemic for injection water in the gas turbine – afterburner. (level laboratory).
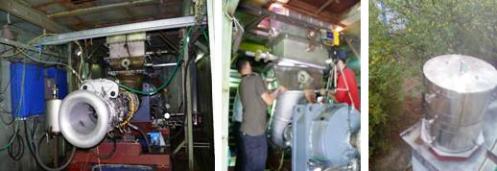
Burst water obtained by pumping water through the nozzle holes corresponding dual atomizer
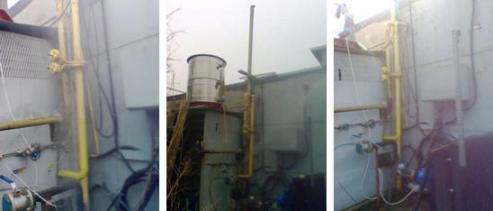
Spray tests with different injection
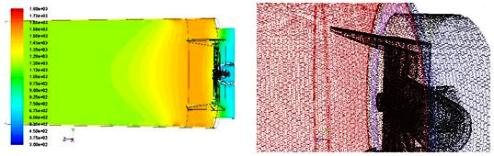
Modeling with different geometries for post - combustion burner
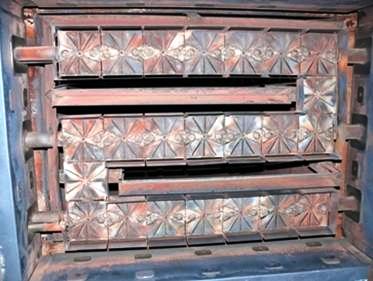
Modules-afterburner (6 pieces) mounted after approx. two years of operation in industrial conditions
Technical and scientific results of fourth stage is materialized in: TA2 gas tubine on natural gas with water injection and afterburner = 1 pc. (experimental model); numerical model relate to afterburner operation at different flow rates of water injected into the flue gas = 1 pc.; test bench relate to water injection into gas tubine with afterburner = 1 pc; documentation relate to test bench of gas tubine with afterburner on water injection = 1 pc.; experimental data = 1 set; technical project, related to assembly of thermomechanical and automation, for water injection into gas turbine from the Beneficiary = 1 pc; modules of afterburner - spare parts, tested in industrial conditions = 6 pcs; technology systemic for injection water in the gas turbine – afterburner = 1 pc. (laboratory scale); research dissemination work = one paper and one book.