Project Results
The method is based on surface coating with special characteristics. The principle is: for the circumference of rotor is used an abrasive material and for active surfaces of stator (part form rotor) are used a soft material. So, clearance between rotor and stator, witch is the cause of gas dynamics loss, is realized through abrasion and in optimum conditions of operating the clearance between rotor and stator is minim.
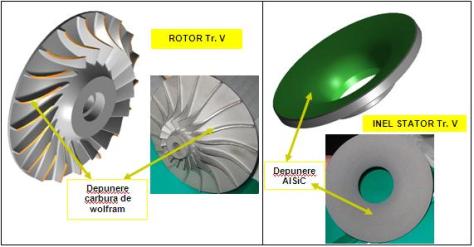
The abrasive coating of WC was realized by ESD (electro spray deposition).
For the stator coating (deposition on the stator internal ring) we used an AlSiC with a 40% C content
The algorithm checking of the productivity increasing for the compressing stage due to the application of a new technique of decreasing the gap between stator and rotor.
The determination of the productivity modification of the compressing stage is made by measuring the gaze-dynamic parameters at the input and output of the compressing stage, in the original version (non-modified) and also in the modified version, after applying the major decreasing techniques of the gap.
It is calculated for both studied cases the adiabatic productivity of the compressing stage and by comparing the two results it is like this checked the improvement level of the productivity; improvement obtained by a sudden decrease of the thickness between stator-rotor.
It results an increasing of the compressing stage productivity of 11,5% which means a relative increase of 11,4%.
It can also be observed an increasing of the air flow with 11,1%
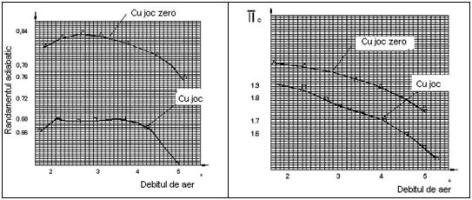
|